The devil is in the details
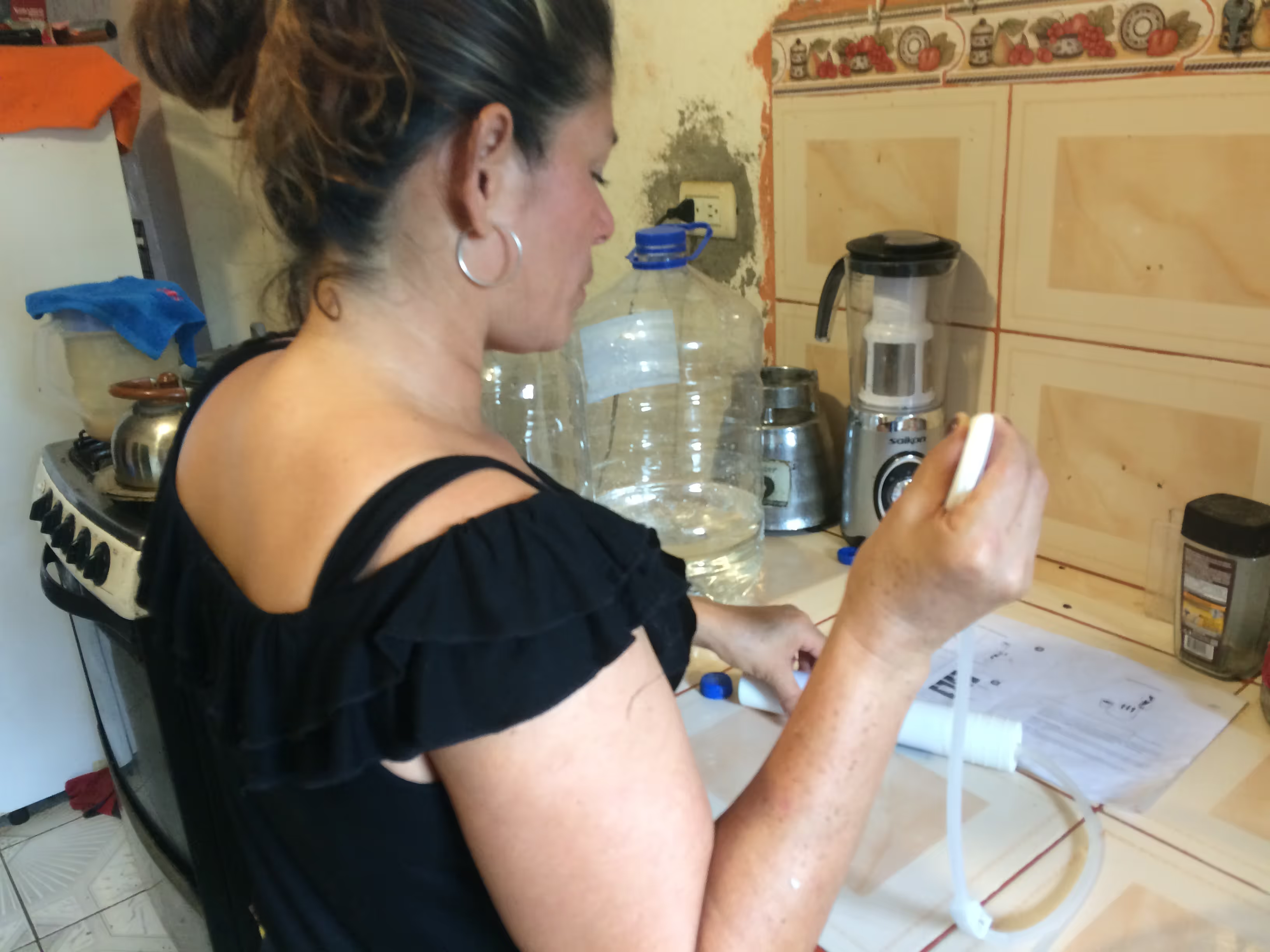
It was a great day when we finally got the prototypes in our hands. Despite delays and malfunctioning parts, our perseverant Head of Research quickly assembled the prototypes, ready for the next steps in our project.
During a team event in a boat on the canals of Amsterdam he proudly presented us with the first prototypes of the Tulip FLOW Siphon. Looking at these nicely shaped water filters made us very excited and obviously we wanted to try them out immediately. Hanging on the edge of the boat we filtered some canal river water, poured it into our glasses and toasted on this milestone. That definitely tasted good!
Not having much time to lose, as we were already behind schedule, we readied the prototypes for shipment to our partners for the field testing. Unfortunately we found out during assembling that not all parts were good and therefore we had to reduce the number of filters being sent to the field by half. We didn’t want to jeopardise anything on safety.

Our field partners in Ecuador, Nepal and Zambia in the meantime couldn’t wait to get started with the testing and selected households in their network who were interested to use the Tulip FLOW Siphon. These households were located both in cities as well as in rural areas.
It was great to be challenged on explaining the water filter and bad internet connections made us come up with an instruction movie. This was initially created for the management of the field testing partners, so they could use it to train the ‘testers’. However, they also used it to show and instruct the users on the Tulip FLOW Siphon. A great addition was that every partner made movies during the hand-out of the filters to the users, so we could see what happened.
First they provided only the manual and the water filter, but gave no further instructions and asked them how they would use it. This gave very meaningful insights in bottlenecks, both in the manual as in the ease-of-use of the filter.
The usage period of one month was an incredible source of feedback. Making use of an app for the survey made it easier for our partners to give feedback on the spot and upload pictures immediately e.g. of storage. In the survey we tried to cover as many angles as possible to get valuable and high-quality feedback both on the technical aspects as well as the ease-of-use, maintenance and design.
Based on the user tests and user experiences it became clear that there were quite some devils in the details. We had to rework the design thoroughly. Though the initial concept stays more or less the same, the physical appearance will be completely different, however still using the same type of membranes. Challenged by time and this very valuable feedback we went fully driven through an intensive re-designing process, which we are currently fine-tuning.
And in the meantime we look up and see the next horizons coming : connecting to suppliers and have the moulds made. The actual preparation for production. We can’t wait!
Stay updated
Sign up for our newsletter to receive regular updates on resources, news, and insights like this. Don’t miss out on important information that can help you stay informed and engaged.
Related articles
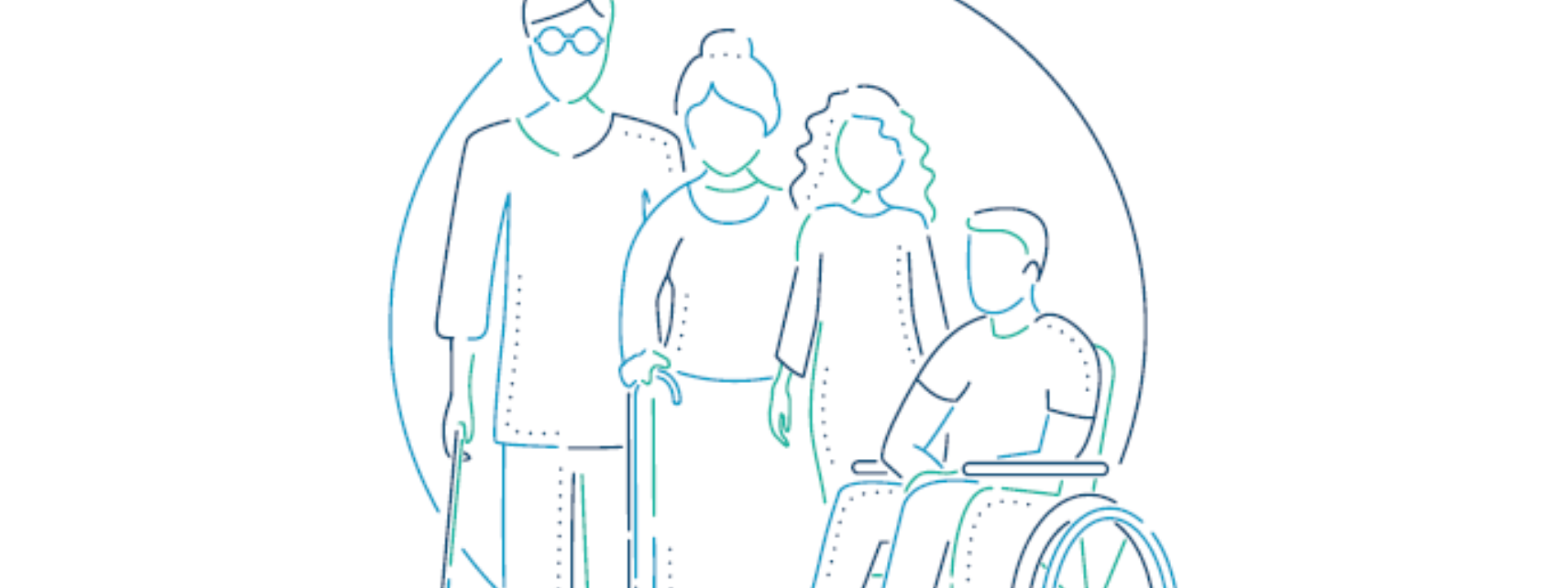
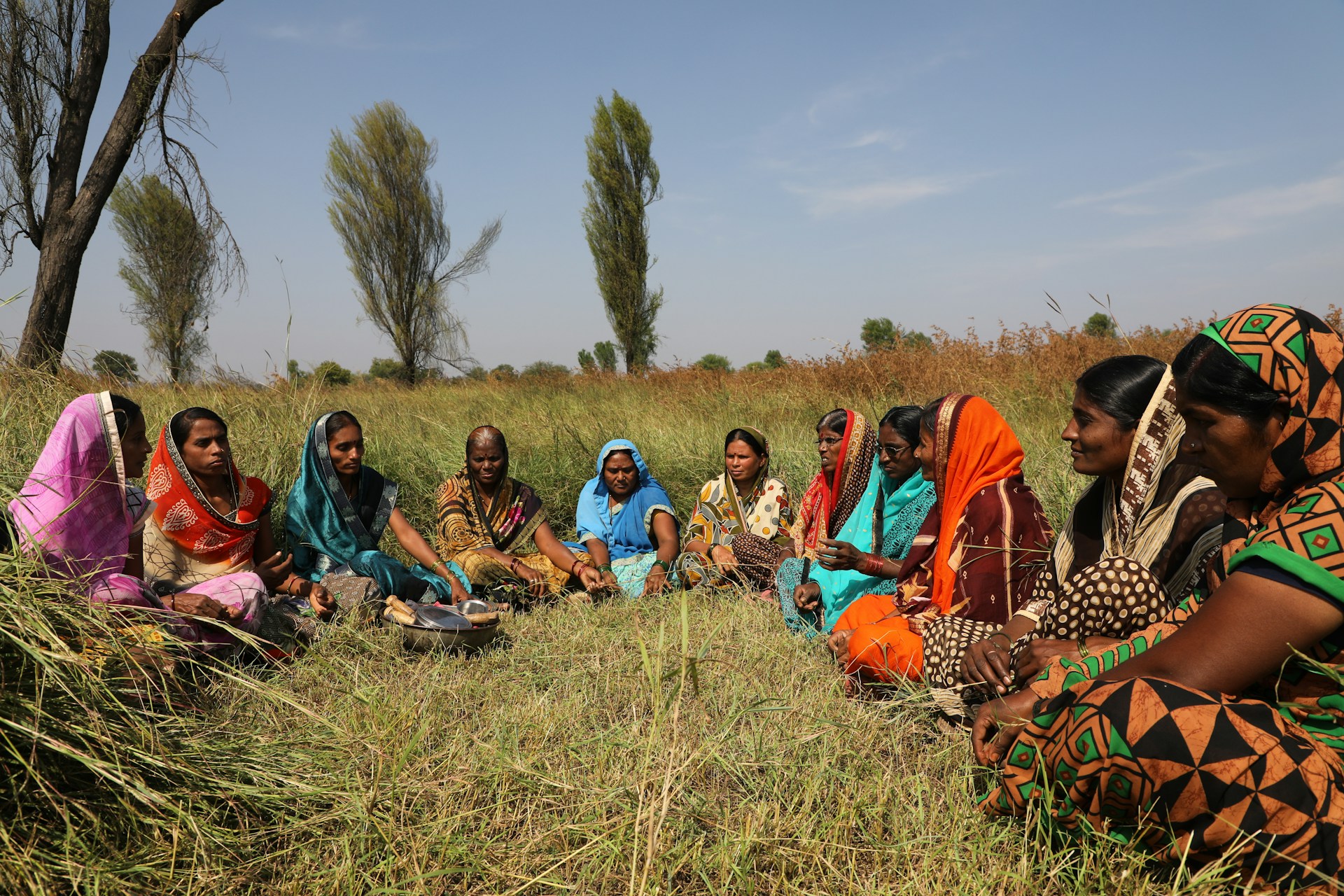
.png)
Explore Elrha
Learn more about our mission, the organisations we support, and the resources we provide to drive research and innovation in humanitarian response.