Griffith Uni - Challenges with the printer
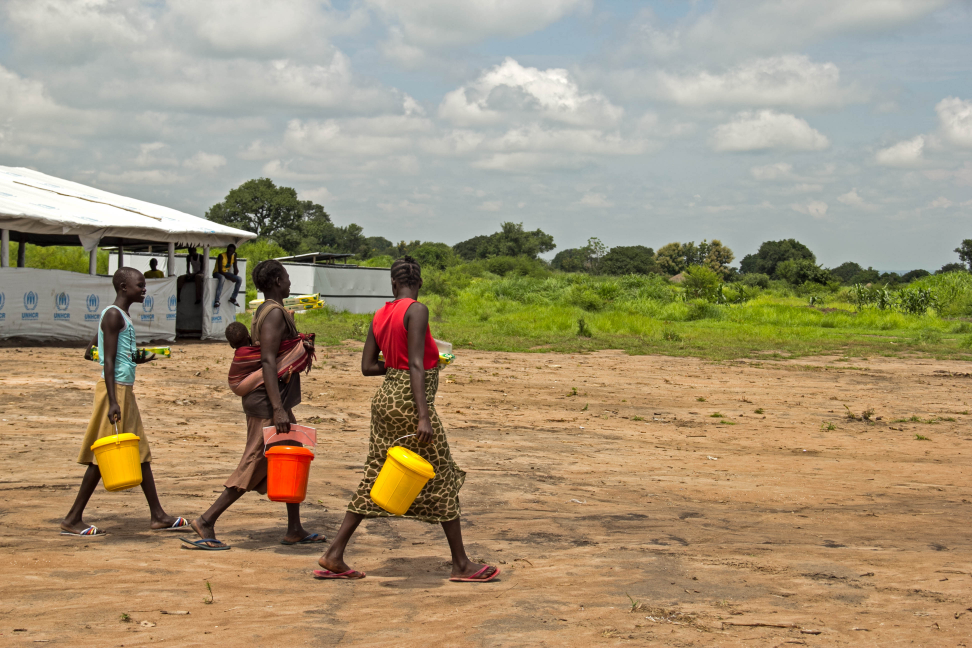
As the 3D printer was running daily in Kenya, we were expecting that it would have some technical problems. Although Ry had familiarised himself with its workings prior to the trip by pulling the printer apart numerous times it transpires that this was a wise precaution as he was faced with two main printer malfunctions over the month of his stay.
The first was apparent due to a funny clicking sound, which led him to discover that the printer was moving around in accordance with the program but printing absolutely nothing! It quickly became apparent that the extruder was no longer being fed with the ABS filament (i.e. the strimmer wire!!) that is needed to create the print. Upon further inspection it seemed the angle the filament was being pulled in was too sharp. This resulted in chunks being taken out of the filament from the teeth on the cog, clogging up the teeth and making the filament too thin to feed down. Fortunately, as a result of his preparatory work, Ry was easily able to pull it apart and clean the ABS. Then, by using a little bit of improvisation with straws and chairs, he was able to get the filament to sit at a better angle in order to easily feed through the extruder and continue printing.
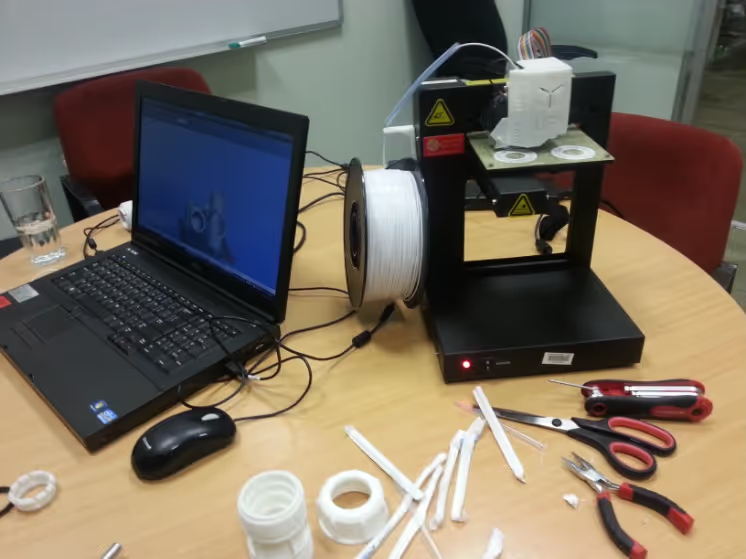
The next challenge was a strange one. Mid-print the printer nozzle somehow moved off the correct path and continued to print a few cm’s off on the Y axis. Upon investigation, it became apparent that when the nozzle is too close to the bed the ABS creates bumps from all the pressure. Then, as the nozzle continues to build up layers, it becomes more prominent and eventually the nozzle will catch on one. The belt that moves the print bed is not strong enough and so the print head will stay where it is. The printer thinks it is still printing, and so once the axis changes it will continue printing – but it will be in a different (wrong) spot. The solution is that Ry had to become much more rigorous with the print set up and ensure the correct calibration of the bed height.
Whilst in Kenya it was also brought to our attention that electrical generators in field locations run for approximately 10 hours at any one time. Although this problem is overcome in the larger camps where there are multiple generators that cycle in and out of use, extending power generation beyond 10 hours would be unrealistic in smaller sites. From the 3D printing perspective, this means that the 10 hour generator time window may present a limitation on the design/production process. In the longer term we are looking into alternative strategies including UPS, solar power and back-up batteries so we have a larger print time window.
Ry will be returning to Kenya in mid-January 2015 in order to continue the project, with a particular focus on the processes that are needed to ensure the components created by the 3D printer are safe to operate and fit for purpose, as well as the consequential training and education needs of the staff in HQ and field locations.
We would also like to take this opportunity to publicly thank all of the Oxfam staff – and in particular Jack Chow as the WASH coordinator - for their total support and interest in the project. As a parting gift we designed and printed off a few ‘made in Nairobi’ water drops with the Oxfam logo as a token of our appreciation.
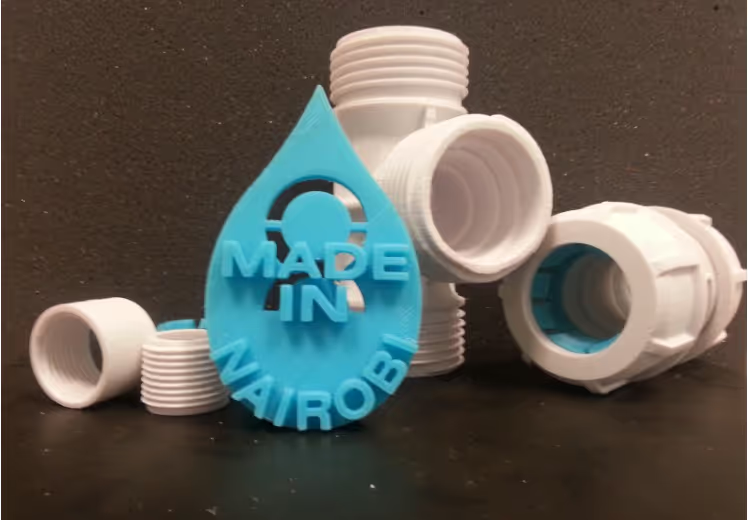
Stay updated
Sign up for our newsletter to receive regular updates on resources, news, and insights like this. Don’t miss out on important information that can help you stay informed and engaged.
Related articles
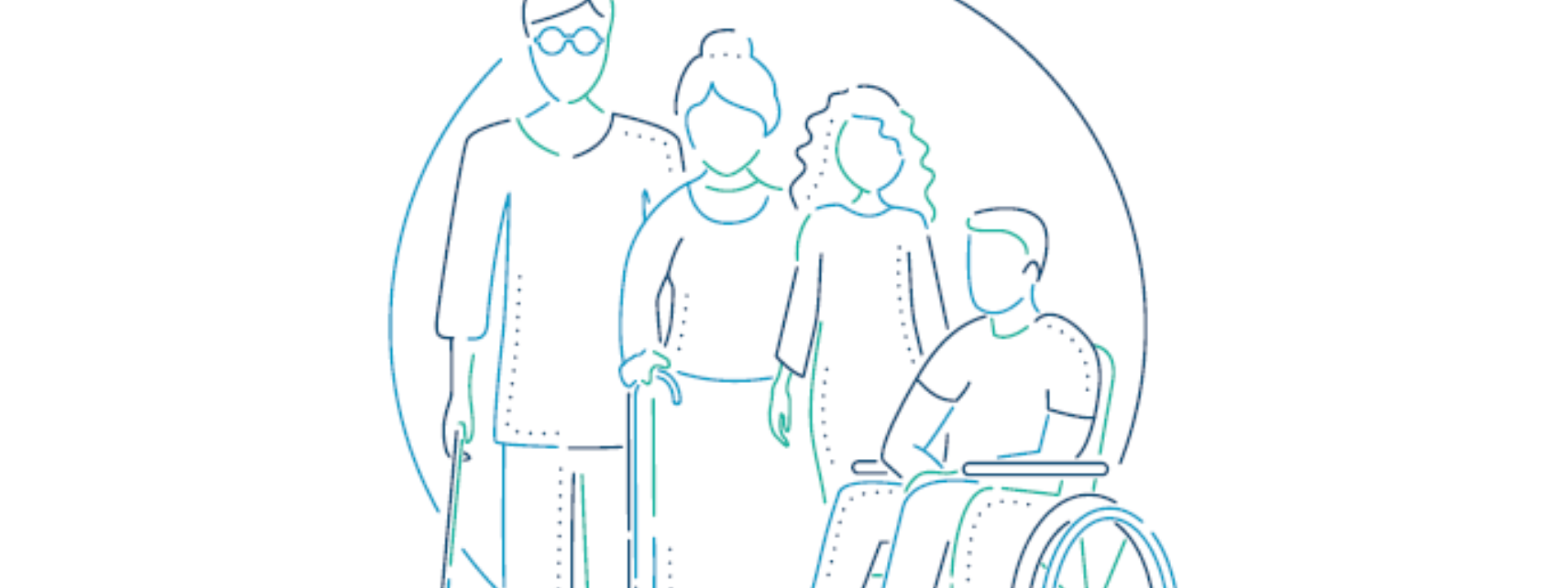
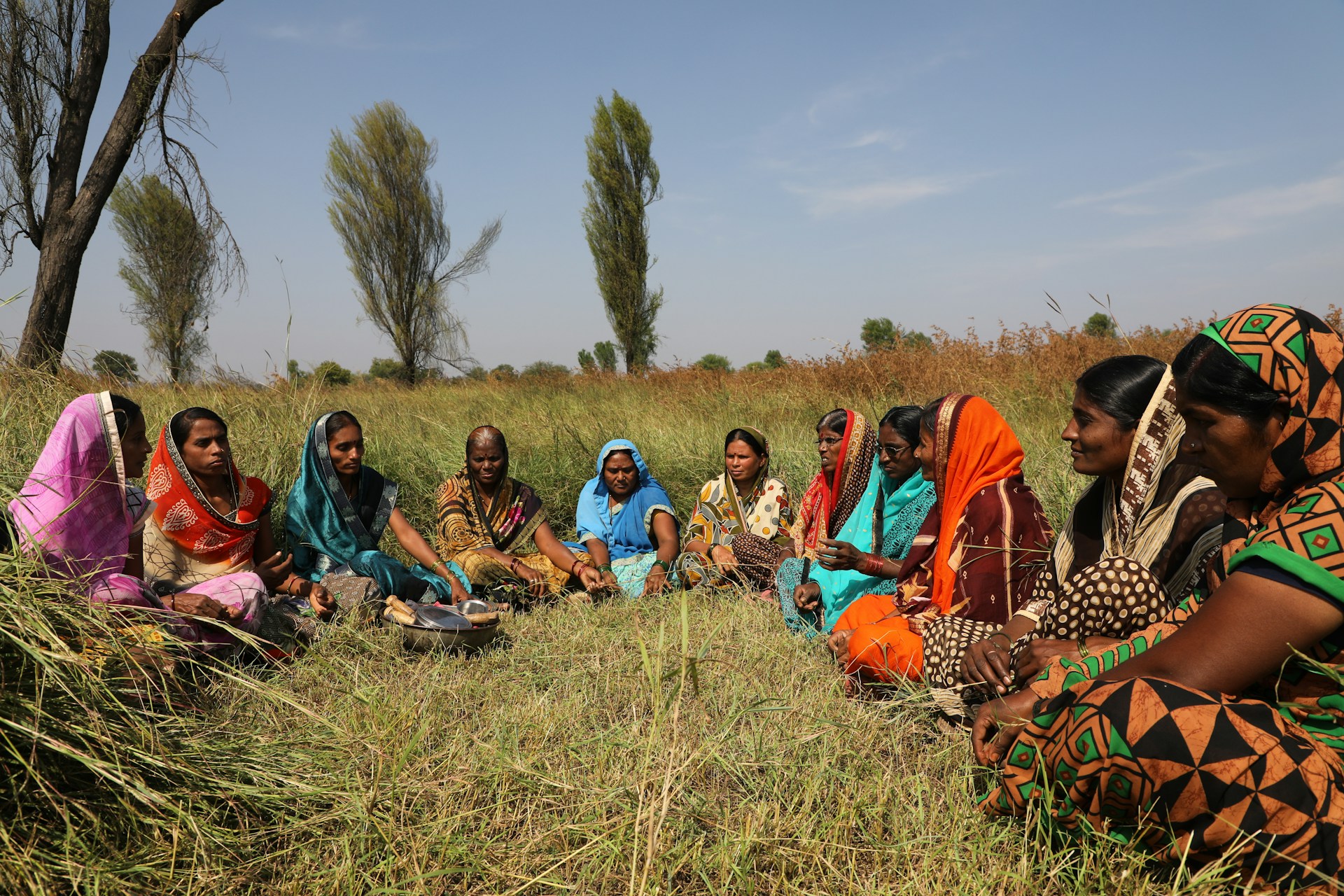
.png)
Explore Elrha
Learn more about our mission, the organisations we support, and the resources we provide to drive research and innovation in humanitarian response.