From Design Brief to a Prototype
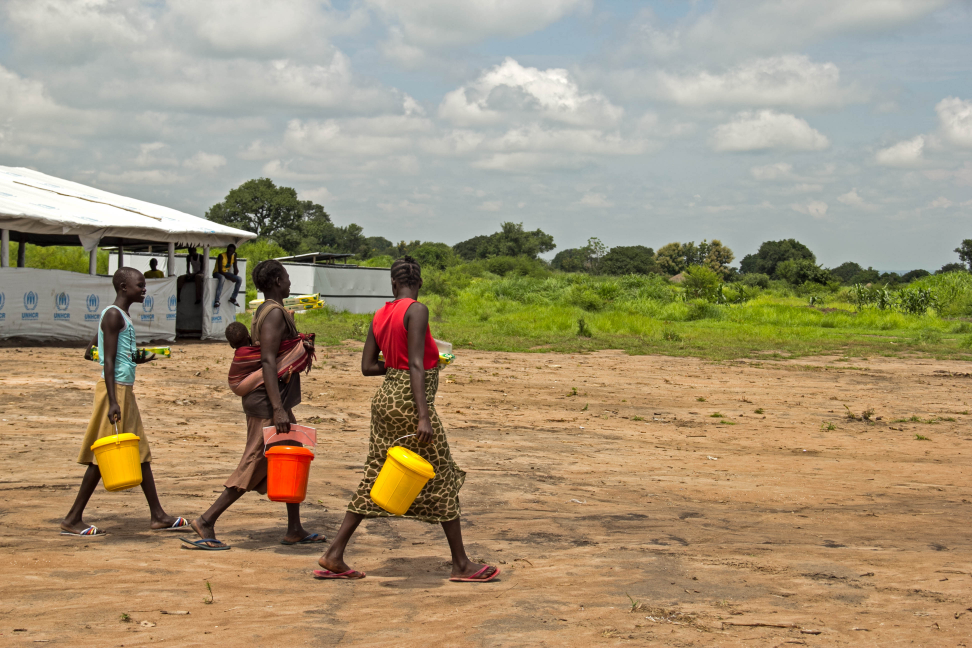
Sarah Sheldon- Programme Coordinator, Motivation
With 34 years of wheelchair design experience between them, engineer Stefan Constantinescu and industrial designer Chris Rushman are more than capable of resolving the inherent conflicts within a design brief for an emergency wheelchair. The wheelchair should be temporary but durable. It must be compact when shipped, but still be able to be adjustedto each user. It must be designed for rough terrain. And all this must be achieved at the lowest cost possible.
To our knowledge there are no appropriate wheelchairs commonly distributed in an emergency situation to people who are injured or have lost their existing wheelchair. People who need wheelchairs become vulnerable as they become immobile, excluded from relief efforts, dependent on others and at risk of serious health complications. We hope to address these problems with this project - reducing overflow in health services, avoiding isolation of injured and disabled people and facilitating mobility in the worst case scenario of successive displacement.
Our starting point for the design process has been to look at various wheelchairs currently being produced. Motivation has been designing appropriate wheelchairs for use in developing countries for 20 years now, and this experience means that we don’t start from scratch each time.
One of the key issues for an emergency wheelchair is cost, and costs can be kept down by using components already in production where appropriate. We’ve been negotiating with suppliers in China, where the majority of factory produced wheelchairs are made, on specific component costs and production volumes.
One of the components we’ve been concentrating on is the folding mechanism. This is a common weak point in a wheelchair, but necessary for this particular wheelchair to enable compact shipping and storage. The folding mechanism needs to be designed so the wheelchair feels rigid and durable once opened out, and does not wear and become loose during use. Stefan and Chris have been testing different designs and have now made up prototypes in the workshop which will be tested in the field trials.
Another decision to be made is the level of assembly of the wheelchair when it leaves the factory. The more complete a wheelchair is when shipped, the larger the boxes will be – fitting fewer into a container and increasing the unit cost. However any assembly needed on location such as fitting push handles or footrests makes distribution more complex and time consuming. We’ve come up with four options of assembly levels which are currently being discussed.
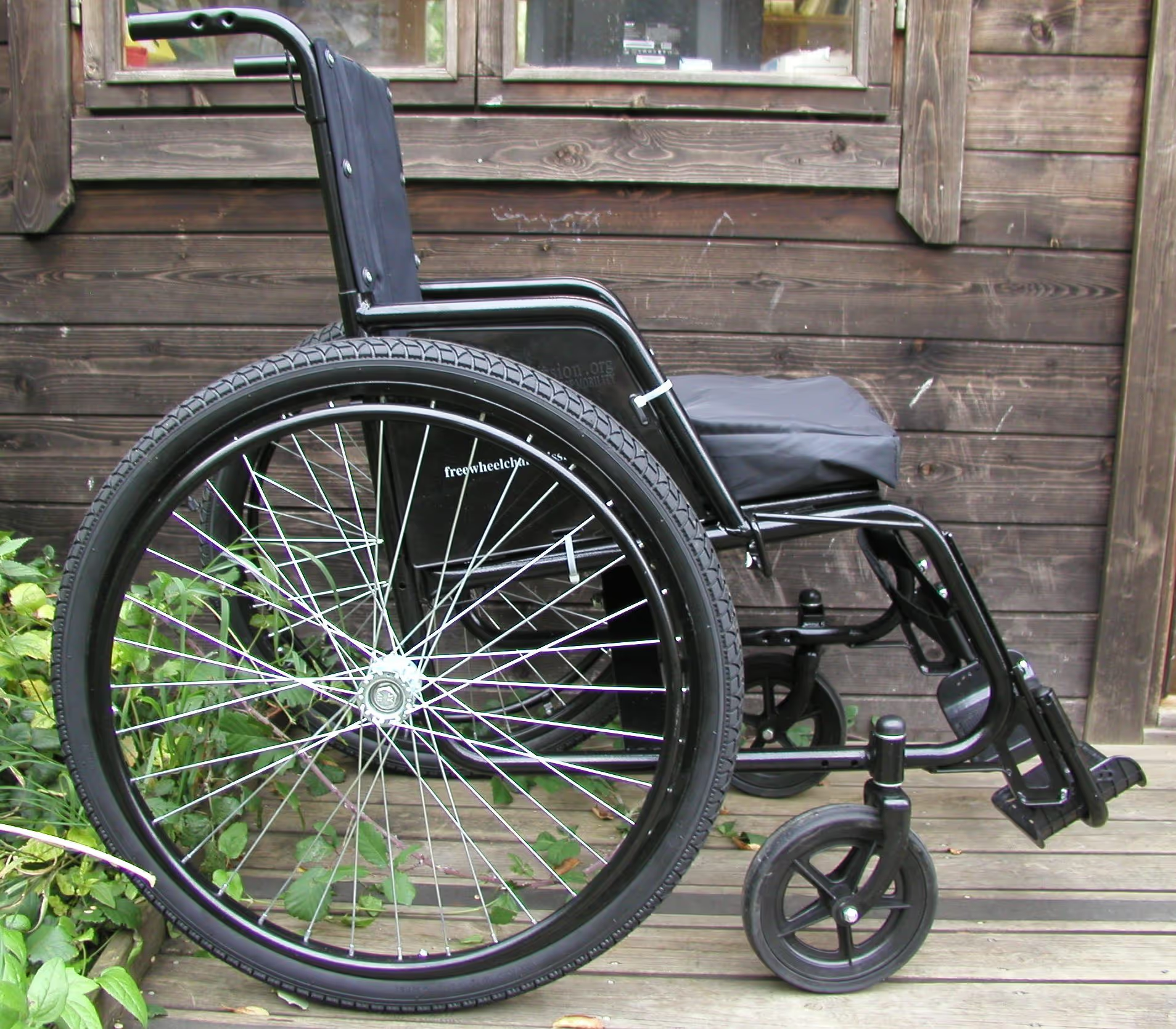
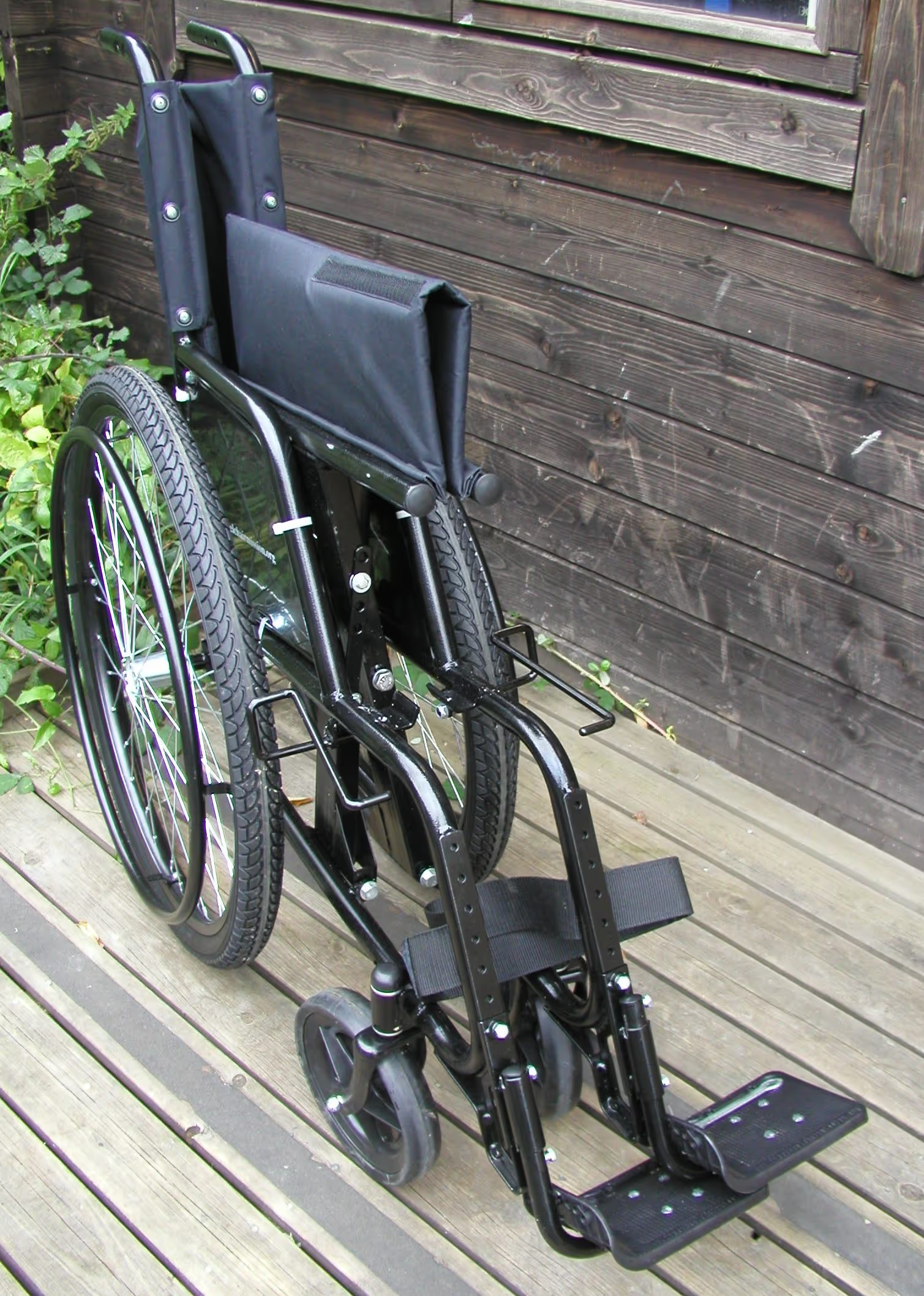
Next week we’ll travel to France to meet with Handicap International – our partner in this project. We will be taking with us two finished prototypes to review - both are a similar design but with detail and cost differences. We need to agree the most appropriate cost and detail level for a temporary emergency wheelchair. The prototype will then be produced in small numbers and we will move forward to the next stage of the project – field trials.
All very exciting - and if we get the design right we’ll be that much closer to meeting our goal of effecting the rapid distribution of wheelchairs in crisis situations.
Stay updated
Sign up for our newsletter to receive regular updates on resources, news, and insights like this. Don’t miss out on important information that can help you stay informed and engaged.
Related articles
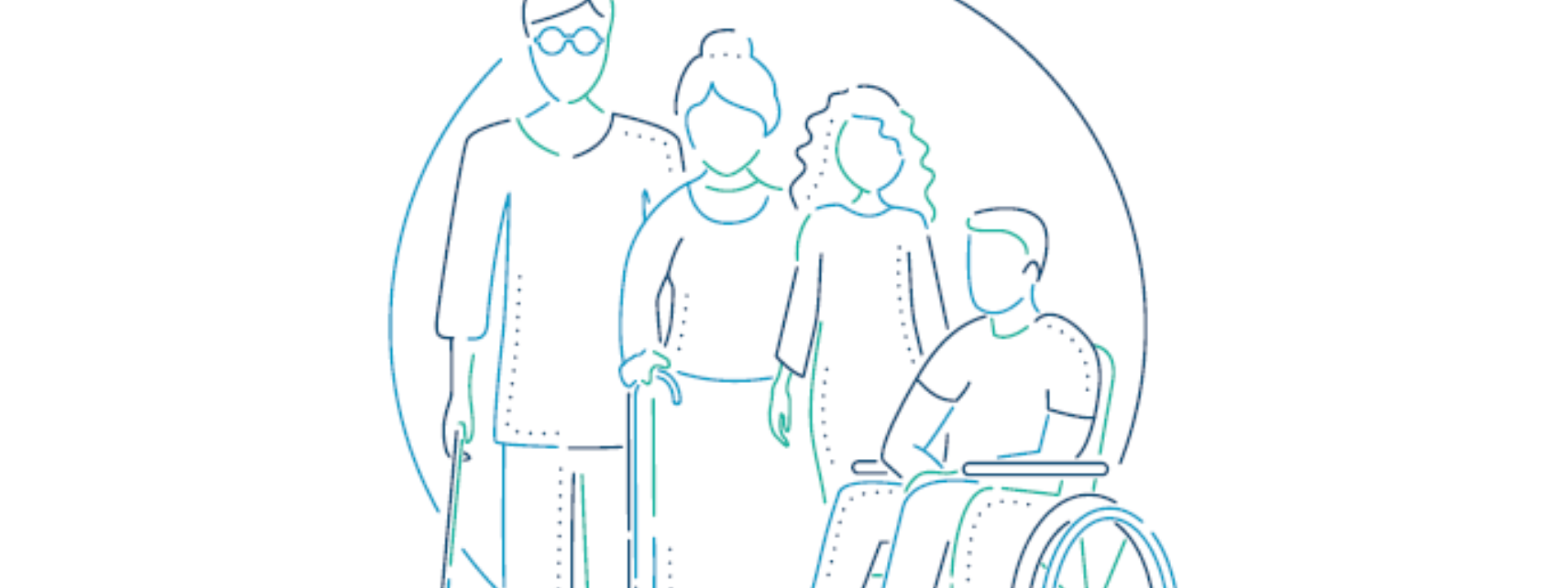
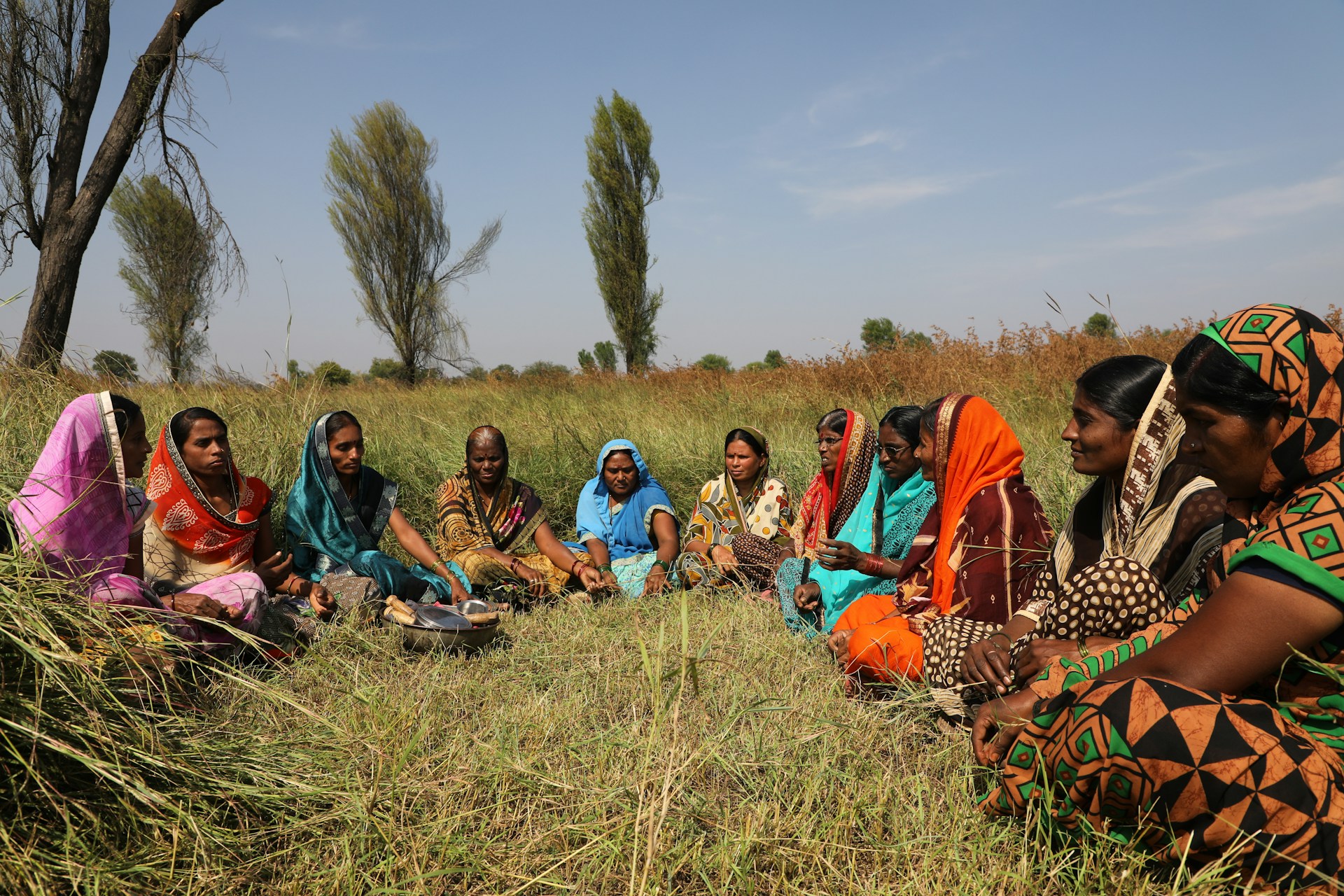
.png)
Explore Elrha
Learn more about our mission, the organisations we support, and the resources we provide to drive research and innovation in humanitarian response.