3d Printing in Humanitarian Projects: Gaining an Understanding
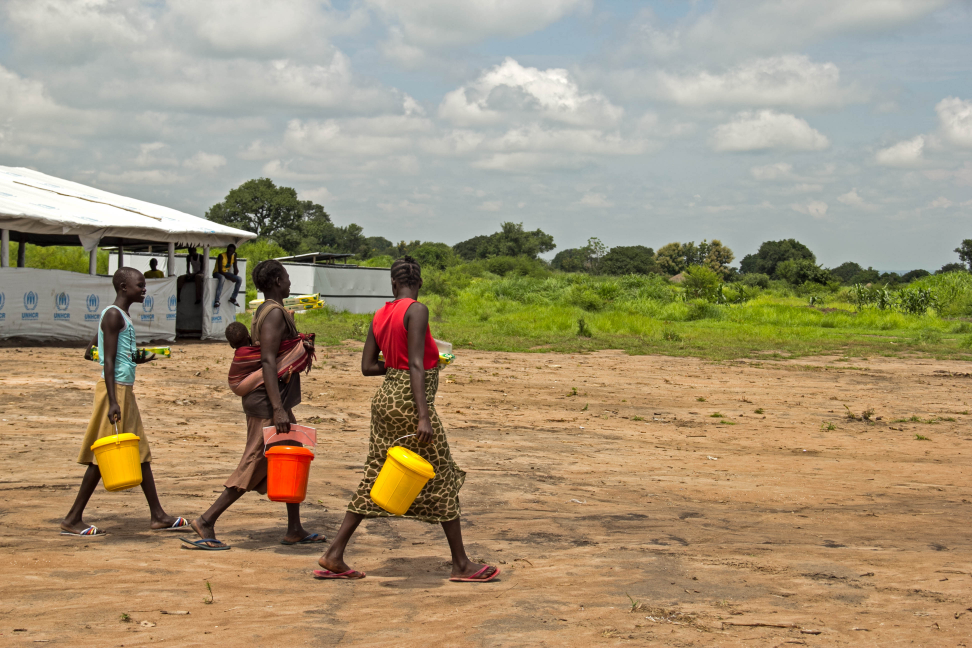
The Griffith University team is four-strong and we come from various areas of the University and with a variety of backgrounds:
Peter Tatham is a former logistics officer in the (UK) Royal Navy who started a second career in academia some 10 years ago. His core research interest is in humanitarian logistics – i.e. improving the logistic preparation and response activities related to disasters, complex emergencies and development activities.
Jennifer Loy is an industrial designer and academic with a specialist interest in digital fabrication, in particular 3D printing. She runs the Industrial design program at Griffith and also the 3D design digital media program and her research is in design for digital technologies with a particular focus on design for health.
Ry Healey is a recent Griffith, QCA, Masters Graduate, whose research lead into the testing and exploration of additive manufacture (3D Printing) and its practical application. He has a background in building design and construction as a draftsman.
Cassie Tapper is finishing her final year at Griffith, QCA, studying a Bachelor of Digital Media Majoring in 3D Design. Her main interest is design for social change, humanitarian projects and 3D printing.
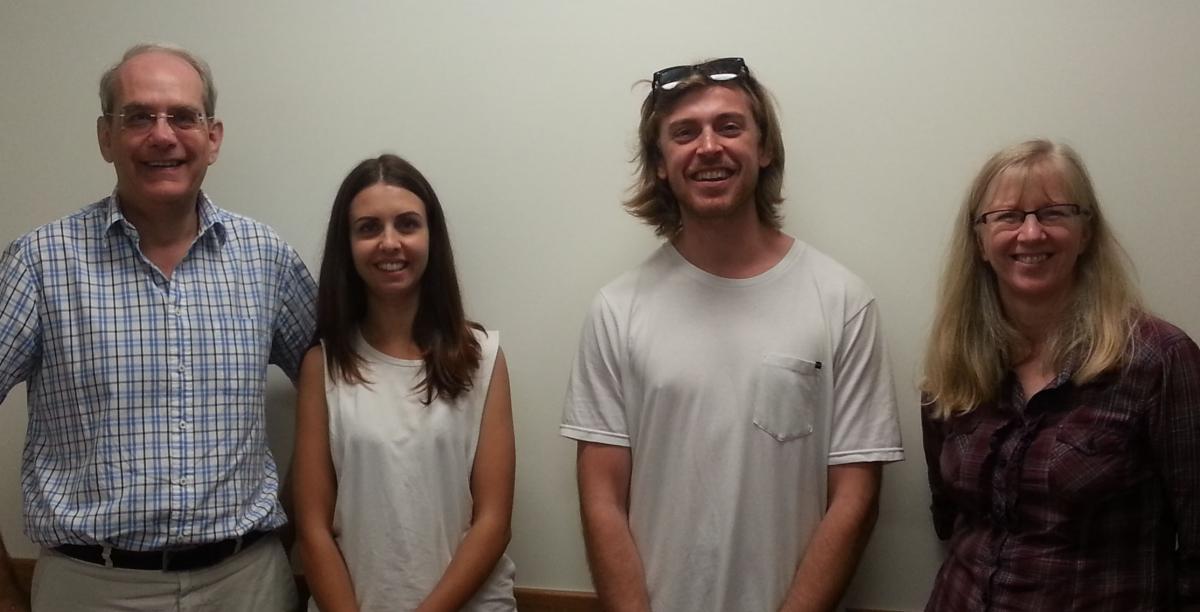
Given these disparate backgrounds and experiences, it was clearly important that we were able to develop an improved understanding of what we would be modeling and printing, and the logistic and downstream training implications.
The first thing that we do know, however, is that we will be using fused deposition modeling (FDM) as our means of manufacture. FDM is a process of laying down the required material in layers from the base up, and we have chosen this technique both for its relative simplicity and also because of its ability to create low cost customizable parts.
There will be a lot of miscellaneous parts that we predict we will end up creating in the field, however to get us started we are focusing on what we know is currently in use. Our partner, Oxfam GB, helped us by sending the full catalogue they use to order parts and, by examining this, we were able to get a good idea of which parts look capable of being 3D printed. Within the catalogue as a whole, our focus is on their Water and Sanitation section as this directly links in to Oxfam’s WASH Programme.
After our initial look through the catalogue, we decided that hose connections form the largest part of what potentially could be 3D printed. But before we attempted to make some, we decided that we needed to see the parts first hand to get a better understanding, so the team went to our local hardware store, Bunnings where we bought a few of the parts that are on our list as candidates for 3D printing.
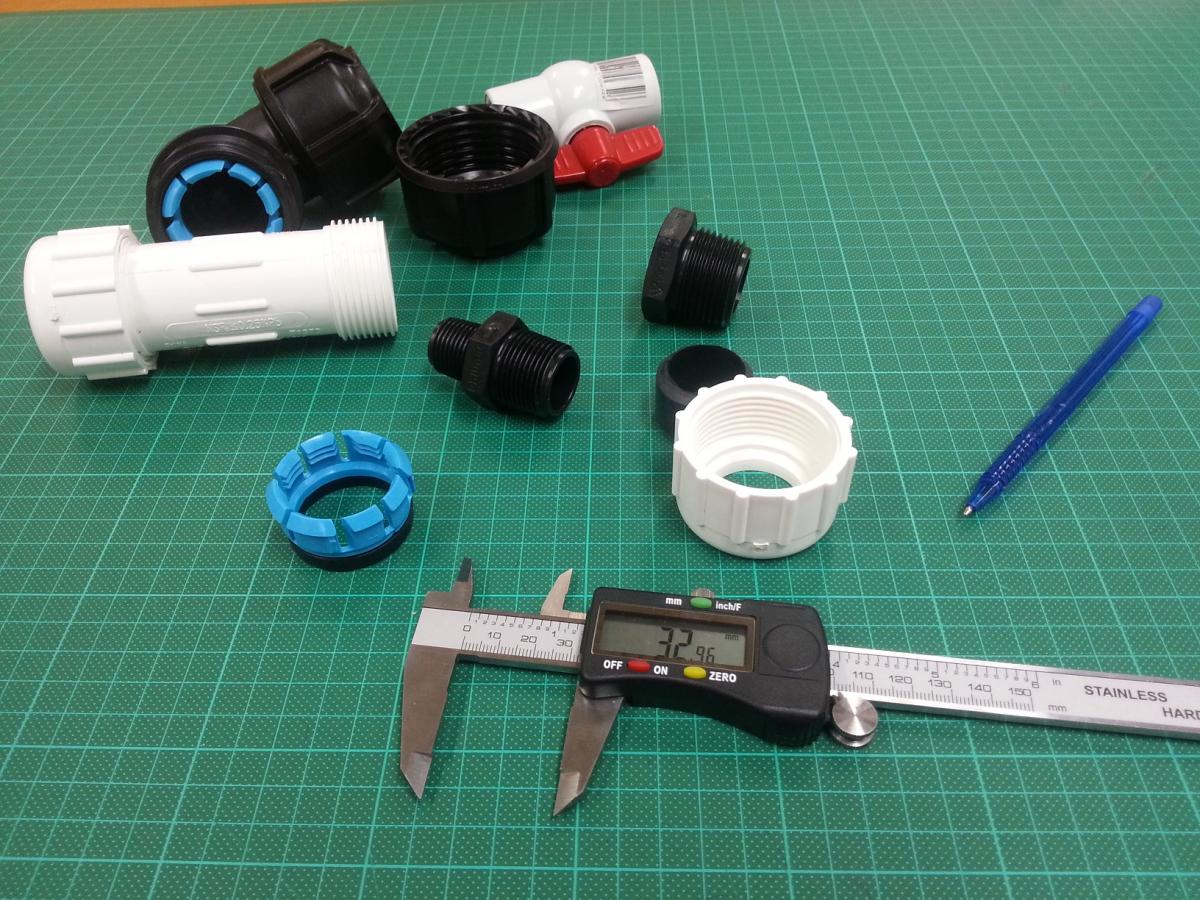
Stay updated
Sign up for our newsletter to receive regular updates on resources, news, and insights like this. Don’t miss out on important information that can help you stay informed and engaged.
Related articles
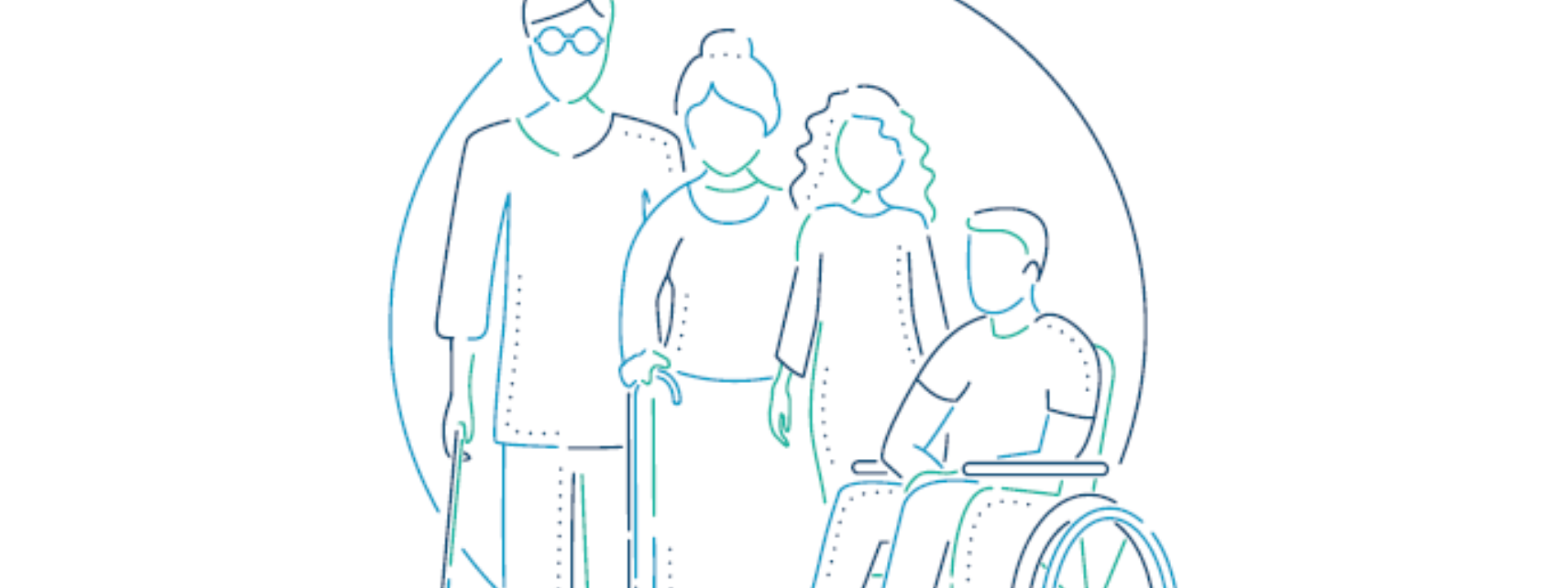
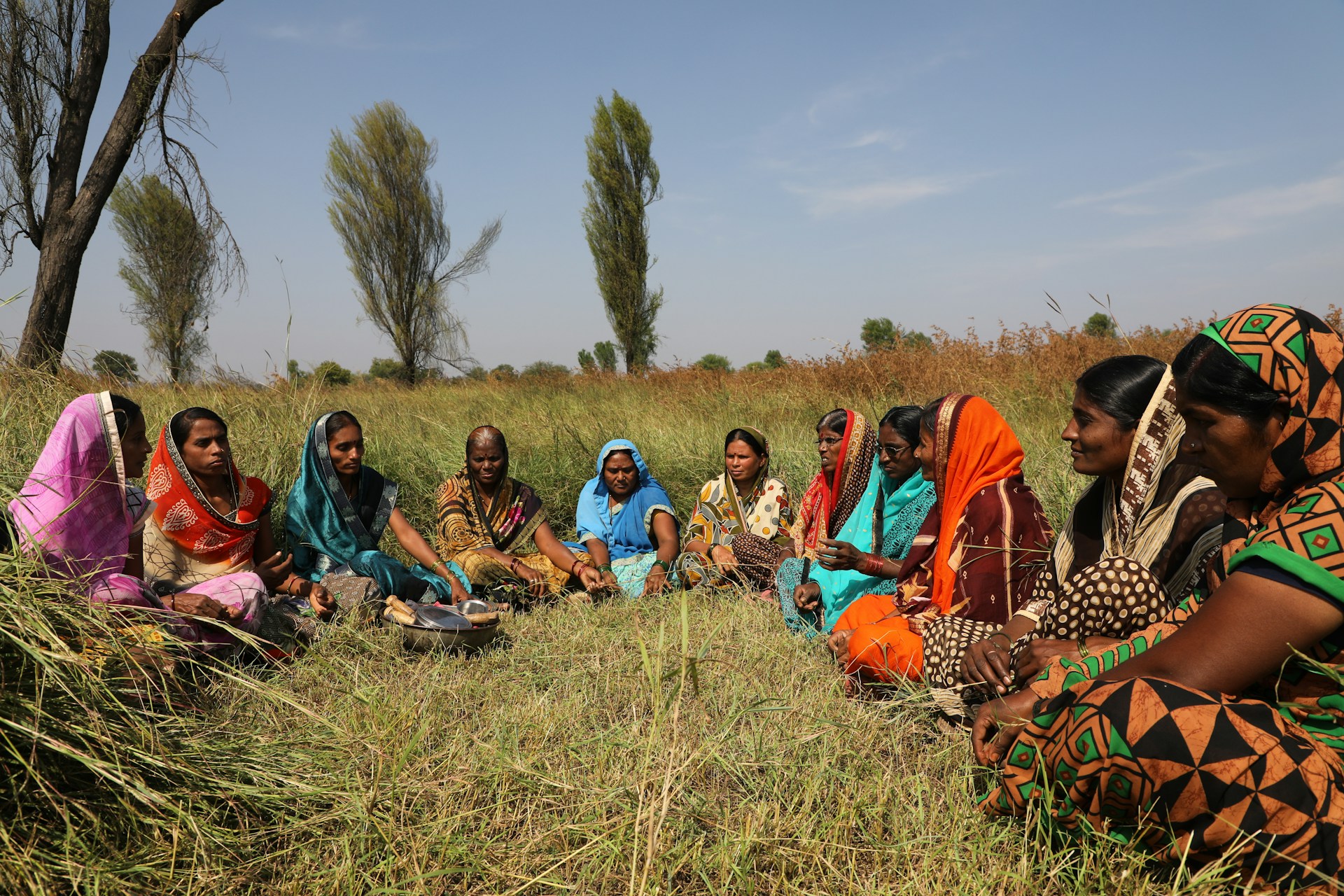
.png)
Explore Elrha
Learn more about our mission, the organisations we support, and the resources we provide to drive research and innovation in humanitarian response.